Data Analytics and Digital Twin
Load Gantry Optimisation and Terminal Operations Enhancement
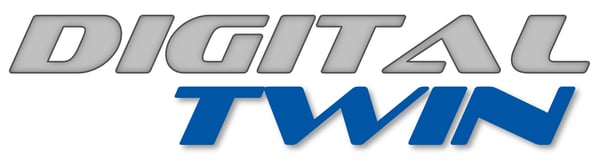
Decouple growth from the resource constraints
DKI's Digital Twin is a digital transformation specifically designed for terminals.
Digital Twin is a data analytics service built for the purpose of enhancing and optimising terminal operation and logistics management. By feeding our proprietary AI modelling system with historic load data, gate-to-gate data, loading process data and other site data we can identify pain points and quantify the gains to reveal the low hanging fruit.
Digital Twin data analytics service enables terminal customers to:
🔹Make better strategic decisions.
🔹Get better control of the operations process.
🔹Achieve cost reductions.
Key Benefits:
🔹Pro-active CAPEX, operations and maintenance planning.🔹Agile investment decisions – direct capex spending to the biggest opportunities by predicting and benchmarking KPI’s
🔹Free up resources – reduce the time required to identify, assess and resolve operational issues
🔹Minimise slow downs – optimise the scheduling of maintenance by predicting the windows that have the least impact.
🔹Reduce unplanned outages – create leading indicators of equipment health so you can take corrective action early.
🔹Manage stakeholder expectations – quantify how step changes in operating conditions will impact performance
🔹Improved customer service – reduce gate-to-gate time and improve customer experience by using optimisation and classification tools to improve loading efficiency.
🔹Optimise storage strategies – monitor seasonal changes in demand.
Operational Benefits
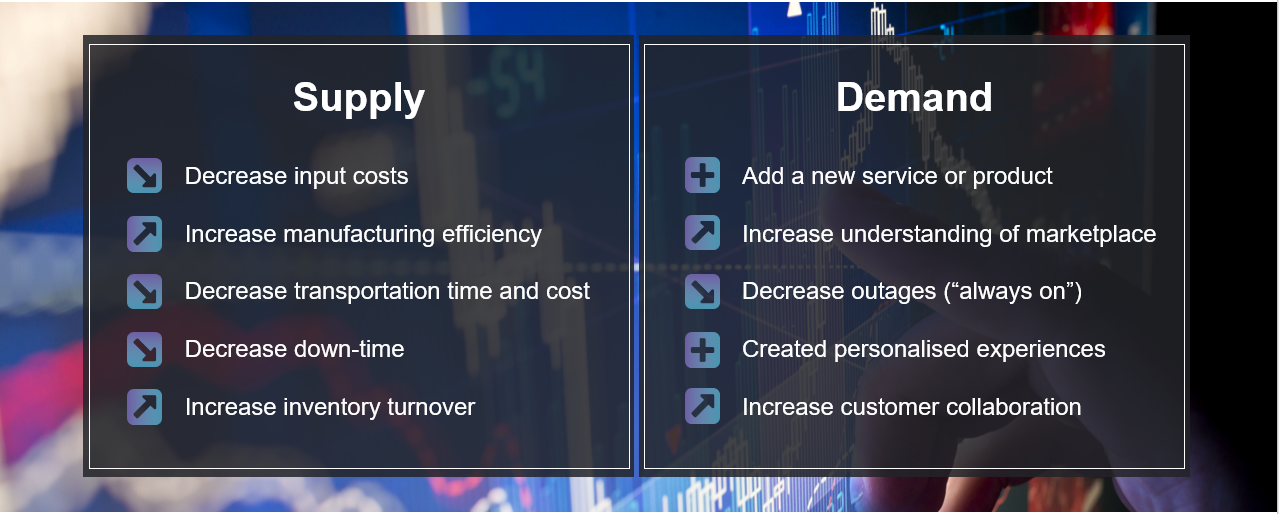
This technology does not function in isolation; it integrates seamlessly with our other innovative solutions:
🔹TIDE: Real-time performance dashboard
🔹FastTrack: AI-powered loading queue optimization
🔹GuardAIn: IoT-based asset condition monitoring and failure prediction
The deployment of our Digital Twin technology offers measurable benefits, delivering tangible advantages for terminal operators, including:
🔹Reduced Operational Costs: Through predictive maintenance and optimised resource allocation
🔹Enhanced Safety: By enabling low-risk training scenarios and remote monitoring
🔹Improved Efficiency: With real-time insights and automated decision-making
🔹Environmental Impact: Through better energy management and reduced emissions
🔹Innovation Platform: Supporting the development of new operational strategies
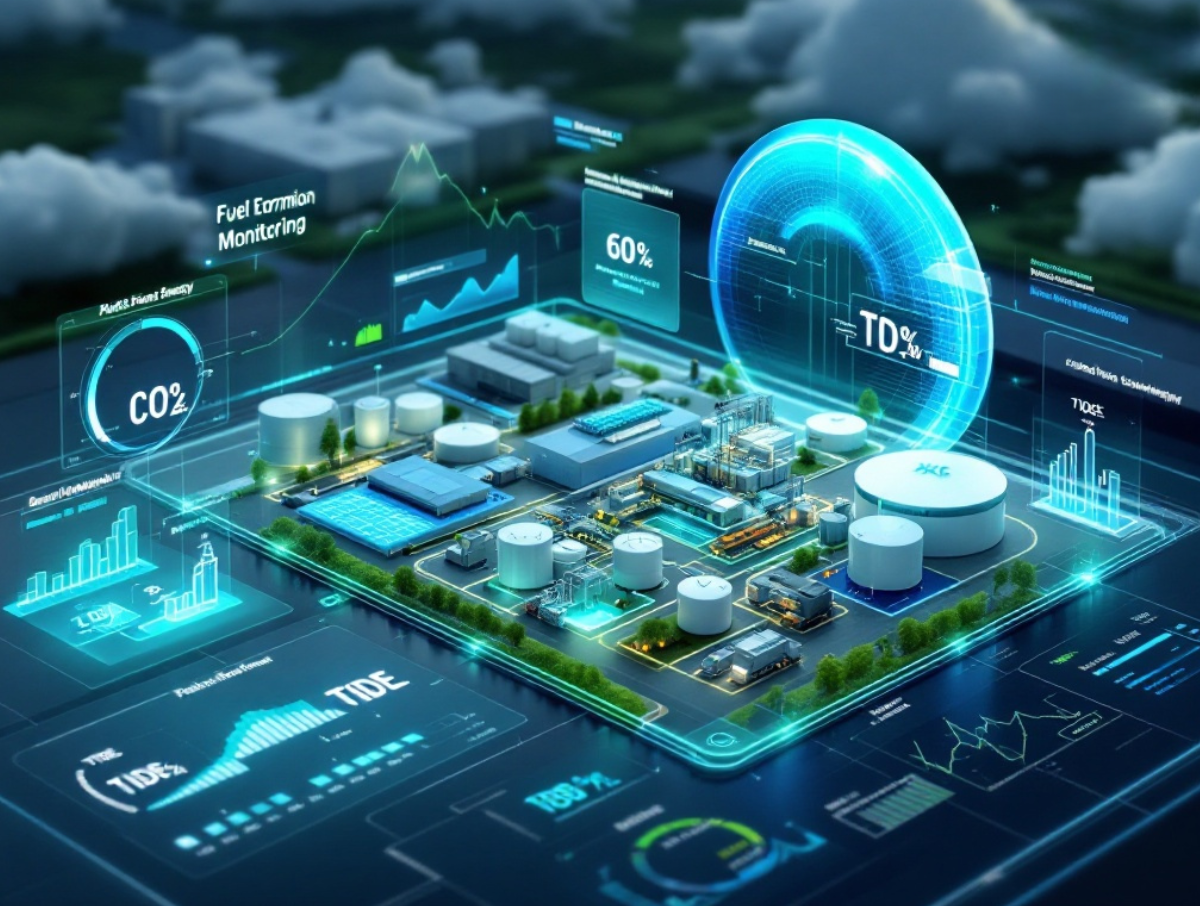
Change produces opportunity. Be the first to capitalise with Business Intelligence.
Business Intelligence module is where our team analyses changing markets, competitive landscapes and customer demands in relation to the terminal. Designed to provide the information terminal operators need to make better decisions in turbulent times.
Case Study: DKI saved CAPEX investment of over $1 million AUD
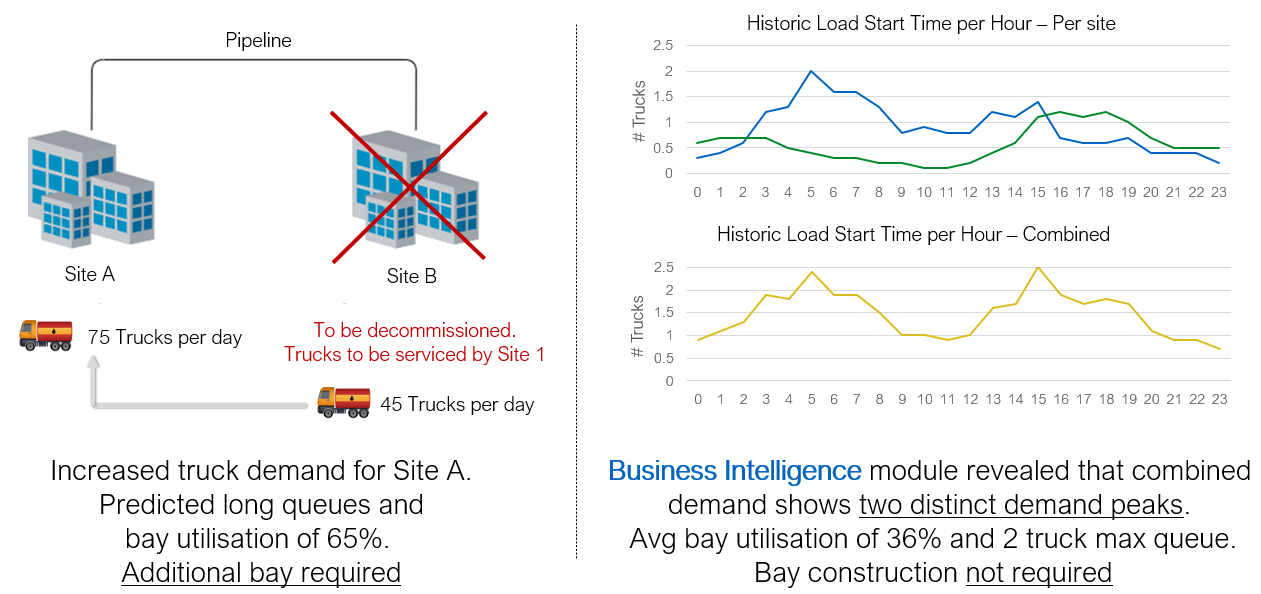
Alarm Analysis - Death by 1000 cuts
Alarms that stop charging are essential for safety, product quality, and product security. But if left unchecked, they can lead to tremendous waste. Our data shows that on average, loading times are increased by 15-25% due to alarms.
The Alarm Analysis module is designed to to identify alarm root cause and provide remediation advice. By using historic loading data alone, our team will identify problems with system fault, driver error, truck fault, intermittent outage and future failures.
Case Study: Alarm Analysis identified 10 trucks responsible for 54% of interlock trips
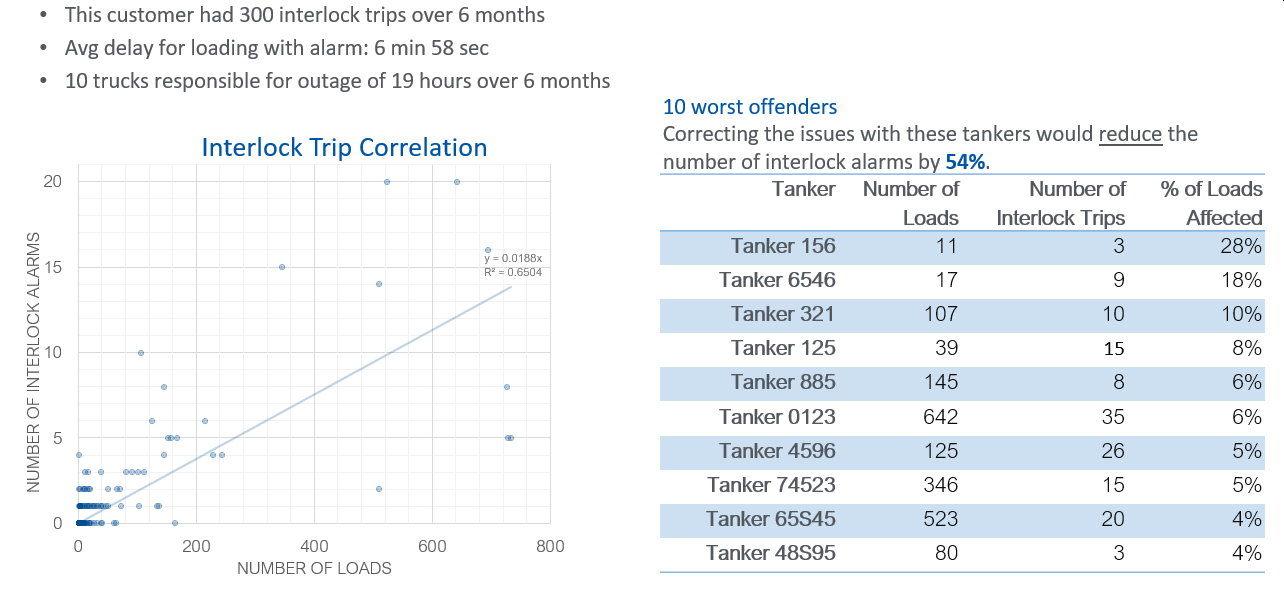
Predicted outcomes and certainty with Digital Twin
By creating a virtual terminal powered by AI, our team will be able to predict the outcomes of changes at site. By pairing this with our expensive knowledge and expertise of the terminal operation, DKI can provide solutions which are cost effective.
This module is particularly effective at eliminating decision risk of CAPEX investment and providing certainty about terminal potential and future throughputs.
Case Study: ExxonMobil achieved a 10% reduction in total loading time by adding three diesel arms to specific bay.
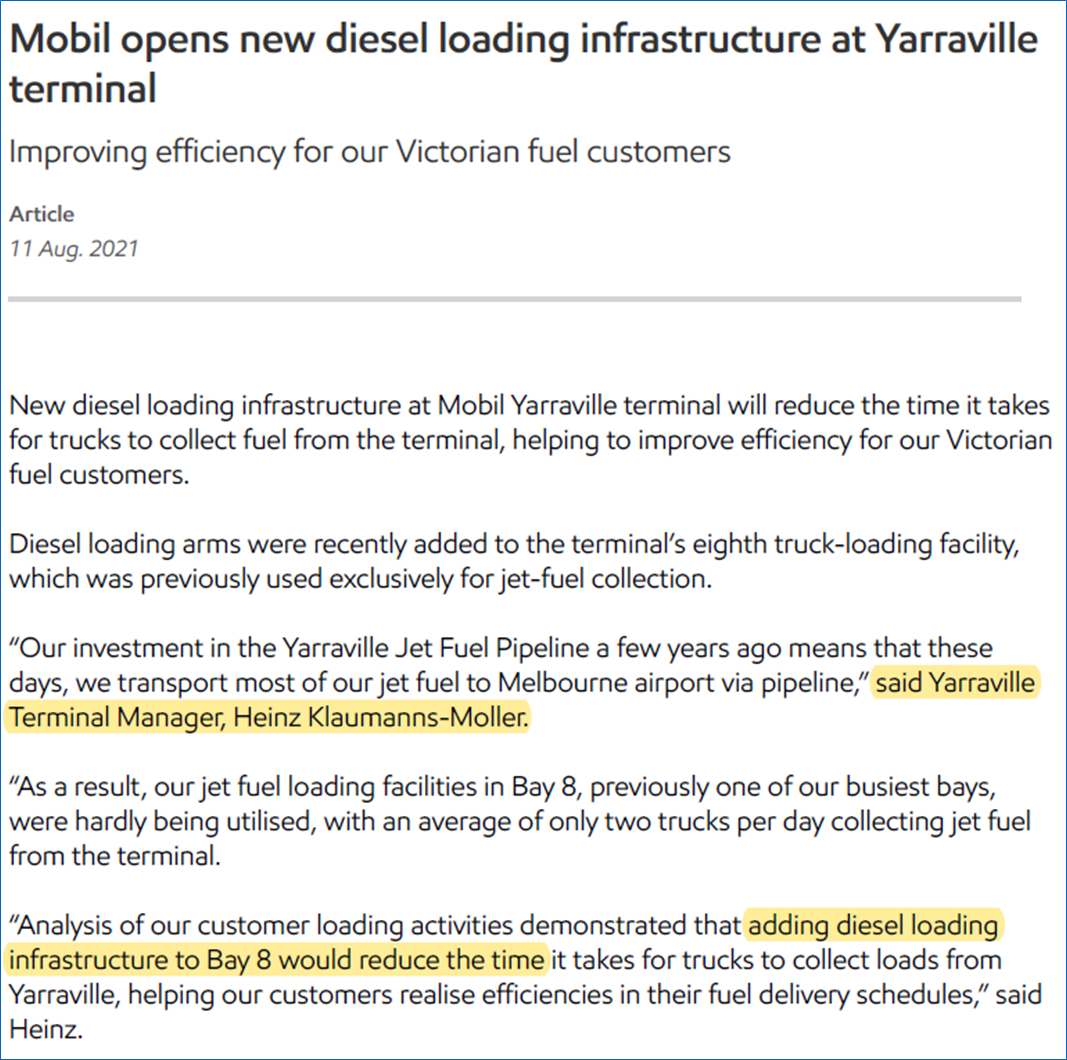
Case Study: Digital Twin saved $1.25million CAPEX by reducing wait times and queues
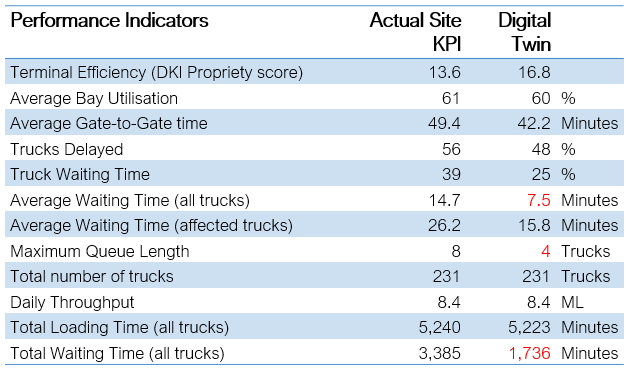